Thermoplastic starch (TPS): A green, biodegradable plastic
Author Dr. Bettina Plaumann
As pollution from petroleum-based plastics has continued to grow, so has interest in biodegradable materials capable of replacing these synthetic, single-use plastics. Thermoplastic starches, or TPSs*, are an increasingly popular solution to the challenge of sustainable plastics. These materials are biodegradable, come from inexpensive and renewable sources, and can be processed with methods and machinery already in use for synthetic plastics.
In this article, we’ll cover the basics of thermoplastic starches, their advantages and disadvantages, and many of the types of thermoplastic starch and thermoplastic starch blends that are available today.
*Not to be confused with thermoplastic styrene, a petroleum-based thermoplastic elastomer.
What is starch?
Starch is a readily available natural resource that is mainly used by plants to store energy. Crops that are high in starch, such as potatoes and rice, are already widely produced as staple foods, and starch is used in industries ranging from food and flavoring to textiles and cosmetics. Thanks to its natural origins and abundance, starch is completely biodegradable and renewable.
Chemically, starch is a polysaccharide composed mainly of amylose and amylopectin. The long chains and branches of these natural polymers give starch its useful physical properties. The exact composition of a starch depends on the plant that produces it, and so do some of its important properties.
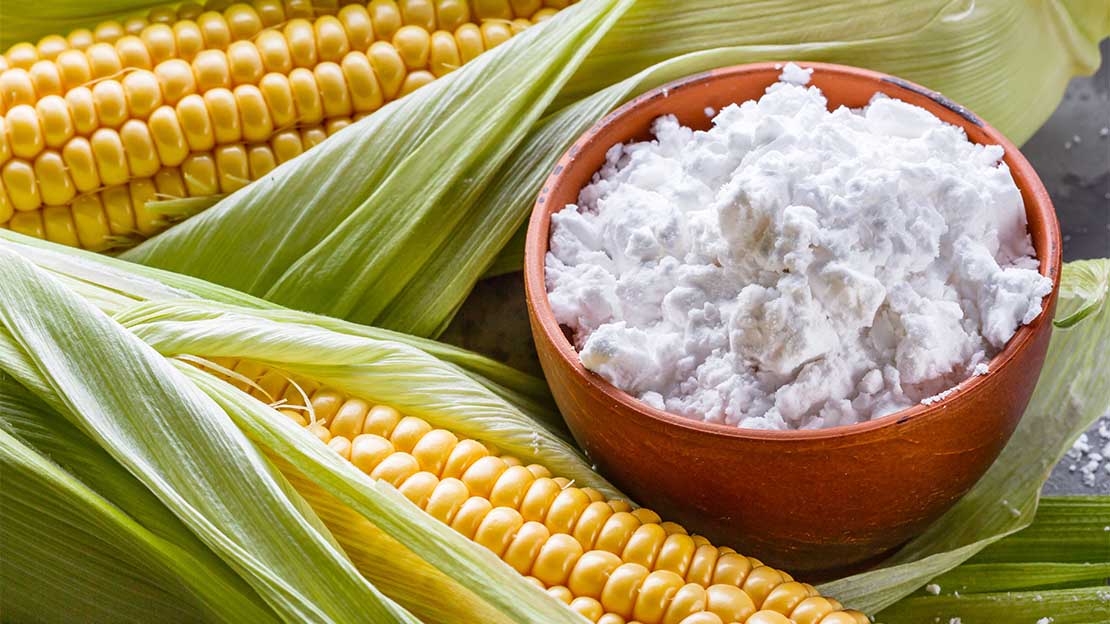
What is thermoplastic starch?
Although pure starch is used in many other applications, it must be processed before it can be used as a plastic. When combined with water and plasticizers (such as glycerol and sorbitol), starch can be heated and sheared to produce a biodegradable polymer known as thermoplastic starch, or TPS.
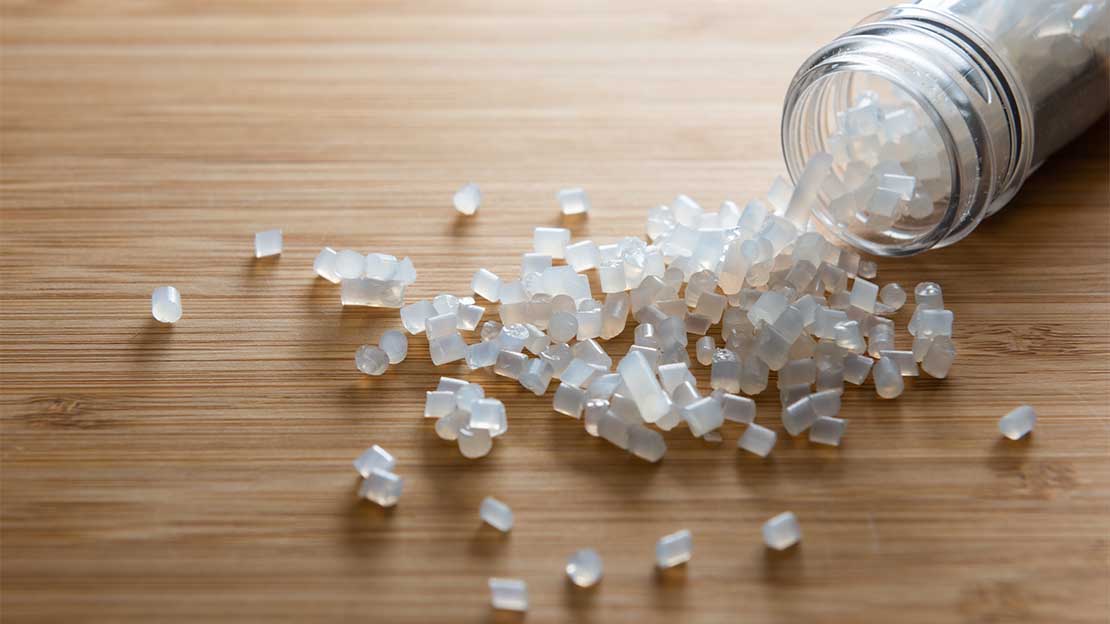
How TPS is made
Thermoplastic starch can be repeatably heated, reformed, and cooled to form a variety of plastic products using existing methods for synthetic plastics. Although its simplest forms exhibit some downsides, TPS is often blended with other polymers to create highly functional, low-cost, fully biodegradable plastics.
Good to know
Starches vary in composition depending on the plant they are sourced from. This introduces an extra level of complexity when producing TPS, but offers a wider range of options for the final plastic’s properties.
Pros and cons of thermoplastic starch
Thermoplastic starch is a promising replacement for many synthetic plastic applications. It is made from naturally occurring and biodegradable materials that are already inexpensive and abundant, making it low-cost, easy to implement, and environmentally friendly.
TPS is also highly versatile and modular. When blended with other polymers, whether natural or synthetic, its properties can be tailored to a wide range of applications. It can also be used in existing plastification processes and equipment designed for synthetic polymers, such as extrusion, injection molding, and blow molding.
When not blended with other fibers or polymers, thermoplastic starches have a few distinct disadvantages. TPS is naturally prone to retrogradation, returning to a more crystalline, starch-like structure as it cools and causing brittleness and poor mechanical properties. It is also naturally hydrophilic, giving it high water solubility and poor water resistance, as well as worse performance in higher humidities.
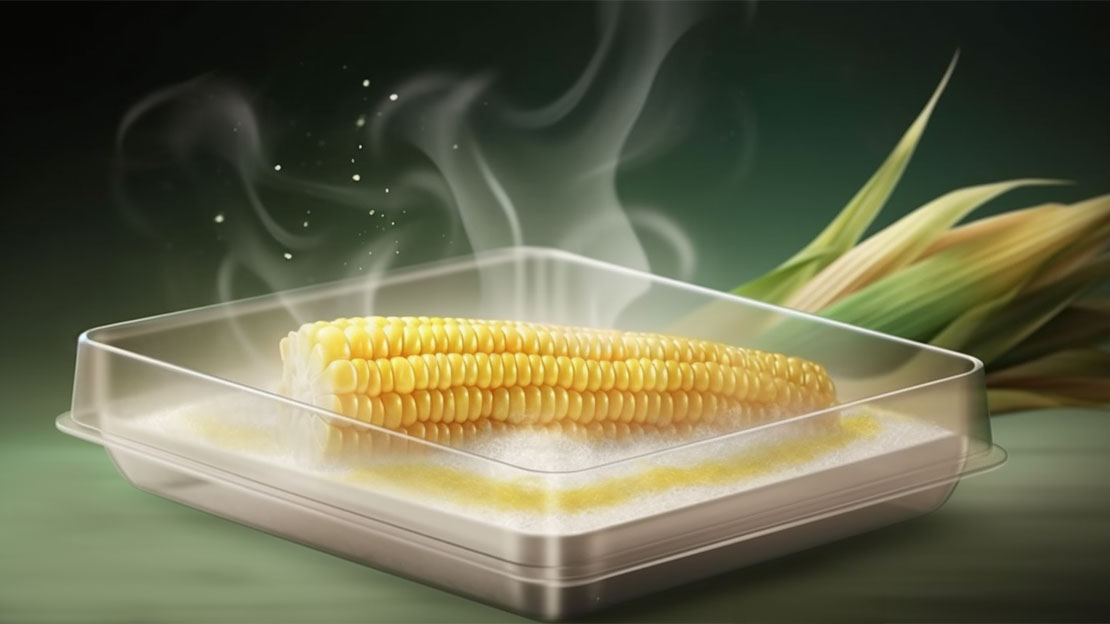
Need a thermoplastic starch without the downsides?
PLANTIC™, the starch-based plastic, is a fully compostable and easy-to-recycle multilayer packaging solution. PLANTIC™ has excellent mechanical properties, doesn’t embrittle over time, and features a PE/PET skin for water resistance. Get in touch with our experts to learn more about PLANTIC™.
Kindly note that we do not sell unmodified TPS.
Thermoplastic starch blends
To address the disadvantages of thermoplastic starch, it is often blended with other polymers to control and improve its properties. By combining strong but expensive polymers with abundant and sustainable TPS, manufacturers can produce a low-cost, effective biodegradable plastic.
Starch x PVA
PVA is a high-cost, biodegradable polymer ideal for packaging applications. When blended with TPS, PVA improves the mechanical and thermal properties of the final plastic while remaining fully biodegradable and decreasing the overall cost. However, the starch/PVA blend remains hydrophilic, and for high-humidity and water barrier applications, additives like glutaraldehyde must be included to maintain its mechanical properties.
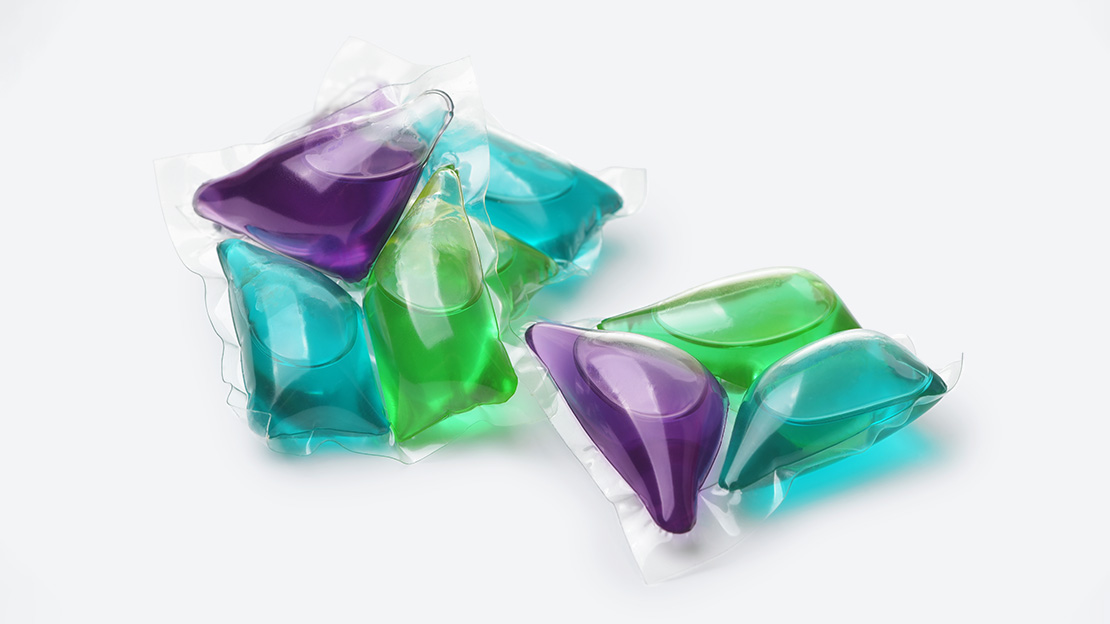
Starch x PLA
PLA is a renewable polyester that forms highly flexible films but is both expensive and brittle. Blends of TPS and PLA aim to eliminate the mechanical downsides of TPS while reducing brittleness and cost. TPS and PLA don’t mix well inherently, but can be effectively blended through co-plasticization and additives such as epoxidized vegetable oils. The resulting plastic has improved strength and is fully biodegradable.
Starch x polybutylene succinate (PBS)
PBS is a biodegradable polyester for applications with good chemical and water resistance, thermal and mechanical properties, and melt processibility. When blended with TPS, the resulting plastic has improved tensile properties and water resistance while remaining both less costly and biodegradable.

Thermoplastic starch incorporated with natural fiber
Biopolymer composites like TPS blends are often strengthened with fibers, which were once mostly synthetic materials such as glass and carbon. Today, natural fibers, especially those sourced from plants, are an increasingly attractive option for many applications. They offer advantages in tensile properties, safety, and biodegradability, as well as lower density, cost, and energy use.
Cellulose fiber
The addition of specially prepared cellulose nanofibers to TPS has several mechanical benefits, including higher tensile strength, lower density, improved water resistance, and improved thermal resistance. Additionally, both starch and cellulose are widely available, renewable, and biodegradable.
Sugarcane fiber
Thanks to the vast quantities of sugarcane produced around the world, sugarcane fiber is an excellent candidate for combination with TPS. Composites of sugarcane fiber and TPS have enhanced tensile strength and water resistance. However, the qualities of the sugarcane used, such as species and age, may affect the quality of the resulting material, making sugarcane a less preferable option.
Cassava bagasse fiber
Cassava is a widely used staple crop that produces a solid, fibrous byproduct known as cassava bagasse. Like many other natural plant fibers, cassava fibers have strong intermolecular interactions with starches, which improve the tensile strength and water resistance of the final plastic.
Applications of starch-based biopolymers
The renewability, biodegradability, and cost-effectiveness of thermoplastic starches make them excellent candidates for any application using high volumes of disposable plastic, especially packaging.
Thermoplastic starches are increasingly popular in applications such as:
- Food packaging (including containers, wraps, and films)
- Disposable utensils
- Protective packaging and films
- Loose fill, antistatic, and formed protective packaging
- Compostable films and bags
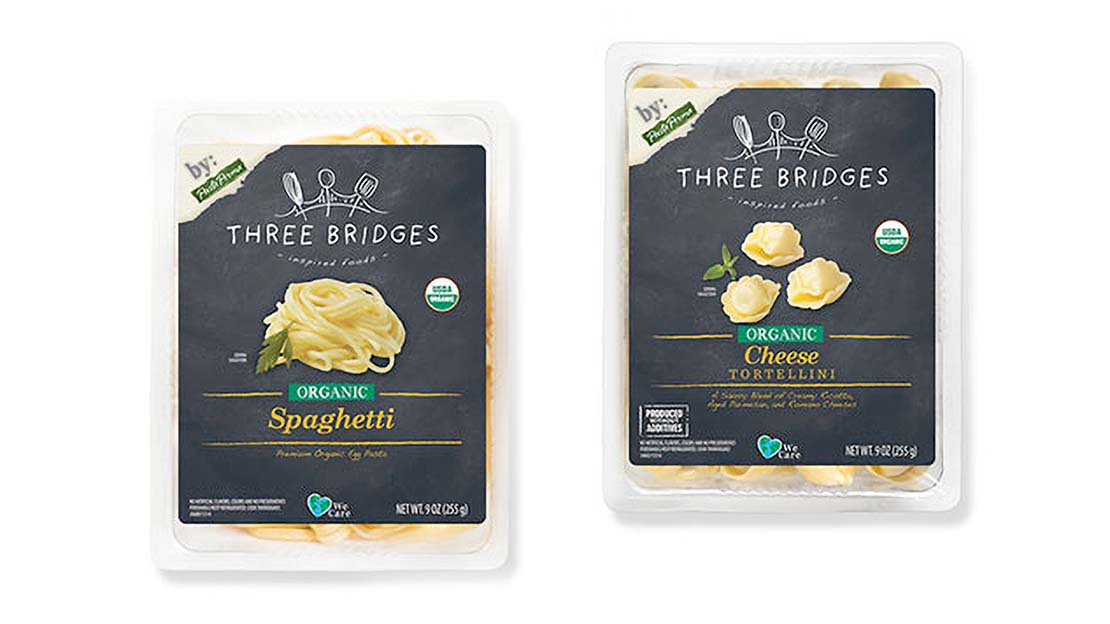
PLANTIC™: The thermoplastic starch-based plastic from Kuraray
PLANTIC™ is Kuraray’s thermoplastic, starch-based plastic for a wide variety of packaging applications. Unlike other TPS products, which are typically plasticized and blended, PLANTIC™ is produced from high-amylose corn starch through a chemical modification process called hydroxypropylation.
This unique process effectively plasticizes the starch, resulting in a material that behaves as a thermoplastic without the usual weaknesses of TPS and can be tailored through additional processes for further improved performance. The PLANTIC™ process provides many advantages beyond just a renewable and biodegradable plastic and a low-carbon production process.
PLANTIC™ does not undergo retrogradation, has excellent mechanical properties, is naturally anti-static and oil resistant, and is sealable, printable, and laser etchable. PLANTIC™ also provides a superior gas barrier and flavor barrier ideal for food packaging, a quality that typical plasticized TPS and TPS blends struggle to achieve.
PLANTIC™ comes in a range of modified starches to meet the needs of a wide variety of end-use applications, spanning rigid packaging, injection molding resins, flexible films, and barrier resins.
Want to learn more? Contact our experts at the link below and ask for PLANTIC™.
Kindly note that we do not sell unmodified TPS.
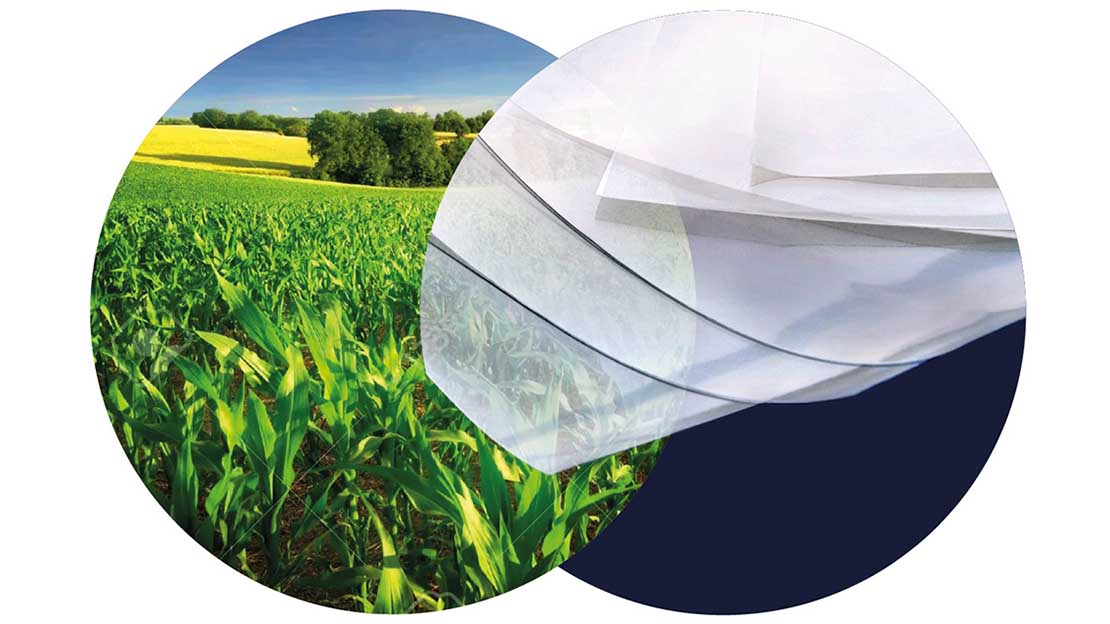